5. November 2024 By Dr. Christian Flechsig
Traceability in production: essential for compliance, cost efficiency and quality improvement
Imagine you are baking a cake. For a good cake, you need various ingredients such as flour, sugar, eggs, butter and milk. You want to know where the individual ingredients come from, how they were processed and how fresh they are. Perhaps you would like to know that the eggs come from happy, regionally-sourced, free-range chickens or that the flour is made from organically-grown grain. But despite the high-quality ingredients, the cake does not turn out as desired. Now you naturally want to know exactly in which ratio the ingredients were mixed, how the dough was kneaded and how long and at what temperature the cake was in the oven, so that you can do better next time. What you want is ‘traceability’ - the seamless traceability of components and processes!
The benefits of traceability in production: quality, efficiency and customer trust
In industrial manufacturing, traceability describes the ability to trace all information about a product, the materials used and the process steps carried out throughout the entire manufacturing process. A traceability system assigns the processed batches to the production orders and processes in order to systematically collect, store, process and evaluate the data. Especially with complex products and processes with a high level of vertical integration, this quickly becomes a challenging task.
An example from the mechanical and plant engineering sector: a company manufactures complex machine tools. One day, a customer discovers that a machine is defective. Without traceability, it would now be extremely difficult and time-consuming to identify the cause of the problem and trace the affected components. However, with an effective traceability system, the company can quickly determine exactly which batches are affected. The system stores detailed data on each production step, from the delivery of raw materials to manufacturing and final assembly. Analysis of this data reveals that a particular component batch from a specific supplier was defective. The company can now take immediate action, inform the supplier in question, start a recall and check the remaining stock. This will limit the damage and maintain customer confidence.
This example shows how crucial an effective traceability system is for quality assurance and risk management in production. In addition, systematic data collection and evaluation supports compliance with legal requirements, customer requirements and industry standards, and enables the targeted identification and optimisation of inefficient production processes, resulting in improved productivity and cost efficiency.
Traceability systems are indispensable in the semiconductor, automotive and food industries, as well as in mechanical and plant engineering. Typically, traceability requirements are implemented with industry-specific standard software. However, these standard solutions often only insufficiently meet the individual requirements and framework conditions of the companies and must be adapted or supplemented by individual developments.
Traceability as a basis for automation and quality improvement: The success story of a global corporation in special-purpose machine construction
The protagonist of our success story is active in special-purpose machine construction and supplies complex systems for semiconductor production. Due to the high legal and customer-specific requirements for product quality and data transparency, all production-relevant information must be seamlessly traceable. The existing standard software is only partially suitable for this due to the company's individual requirements and circumstances. The customer has therefore decided to develop and operate its own traceability system, and we have been providing comprehensive support for this for several years. The powerful system, which is based on intuitive web applications and services, is now making a noticeable contribution to the company's successful development.
Why did the customer decide on an individual development for the traceability system?
- Engineer-to-order production: High-priced end products with their own production process, small batch sizes, complex product structure and a bill of materials with many variants require customised software solutions.
- Necessary traceability of all individual components within the batch: Standard software cannot map the high requirements for data transparency and documentation.
- Highly complex production processes and special machines: Standard software cannot map the necessary manufacturing flexibility and depth (e.g. for rework).
The customer reports significant added value from the traceability system, such as increased product quality, improved cost efficiency and a higher degree of automation.
What added value does the traceability system provide to the customer?
- Enhanced product and process quality: The documentation and evaluation of production-relevant data ( for example, product structure or process chains) in a central system with standardised data structures enables a broader application of data-driven production and quality methods and leads to improved compliance. The traceability system makes it easier to comply with customer agreements in terms of delivery dates, quality and response times, thus helping to increase customer satisfaction and deepen cooperation.
- Significant cost reduction: Early detection and initiation of measures in the event of production problems has reduced scrap rates and rework costs. The increased transparency and standardisation saves redundant efforts.
- Noticeable time savings and a higher degree of automation: Clear web applications and detailed error analyses enable faster problem solving and more effective quality control. The targeted optimisation of inefficient production processes shortens throughput times. The traceability system improves data-driven product and process development and shortens time to market.
To enable the traceability system to deliver this extensive added value, it was anchored at the centre of the special-purpose machine manufacturer's production-related IT landscape – at the interface between the plant management level and the process control level. It is thus directly connected to the manufacturing execution system (MES) and the machine control system (SCADA), enabling comprehensive documentation and monitoring of the manufacturing processes.
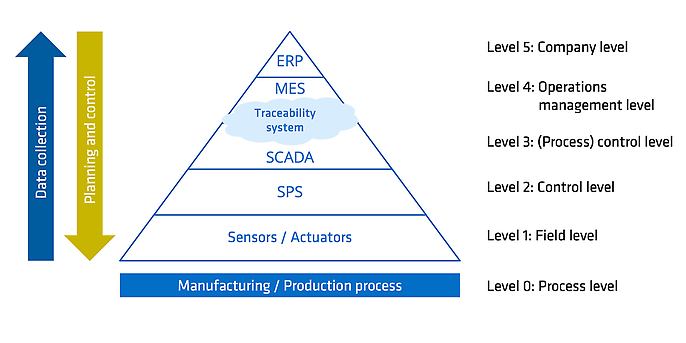
Classification of the traceability system using the automation pyramid
However, for the traceability system to operate, various product- and production-specific features and the resulting requirements must be taken into account. To this end, we continue to provide our customers with comprehensive support in designing the data and system architecture, developing customised applications, connecting to other manufacturing processes and ensuring smooth productive operation.
How did we address the customer's challenges with the traceability system?
- Integration with a heterogeneous, historically grown IT system landscape: Support in developing a powerful database solution with a unified data structure, efficient algorithms and interfaces to machine software and other data-holding systems (such as ERP, MES, customer/supplier systems) to capture, process and transfer large amounts of data consistently and in real time.
- Flexibility and adaptability: Thanks to its service-oriented architecture, the traceability system can be quickly adapted to new products, materials, processes and customer-specific requirements. By means of a comprehensive requirements analysis and documentation of the data and process flows, we improve communication at the interface between the technical side (process development, production) and software development.
- Guaranteeing data security and integrity: Implementing effective business logic always ensures that data is valid and up to date. Comprehensive access management prevents unauthorised manipulation and data loss.
Conclusion: Traceability as a success factor in digital production
Traceability is a crucial building block for effectively digitalising production. Traceability systems enable seamless traceability of manufacturing processes, improve product quality and strengthen customer trust.
Would you like to learn more about exciting topics from the world of adesso? Then take a look at our previous blog posts.
Also interesting:
Have we sparked your curiosity and made you want to learn more about traceability in production?
On our website, you can find out how we support you in the digital transformation of your manufacturing with customised IT solutions and services. I look forward to your message!